Jidoka in Lean: Meaning and Examples
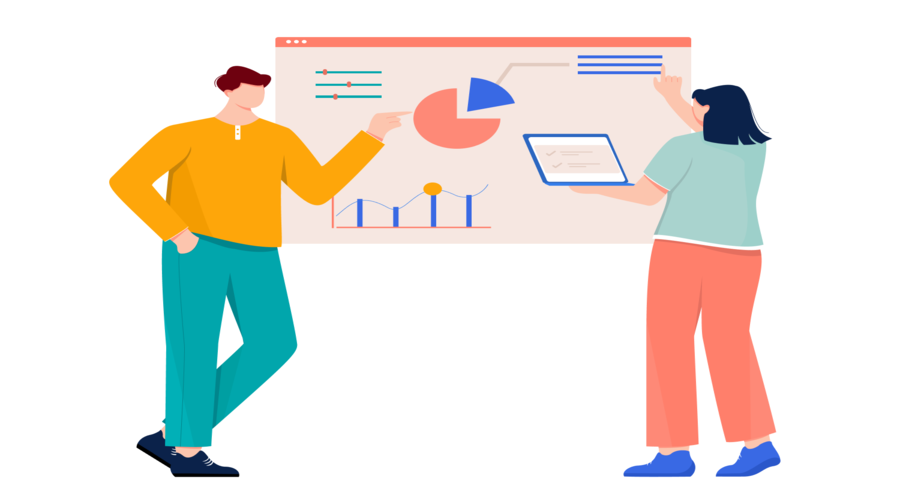
Jidoka is a lean manufacturing phrase that is one of the pillars of the Toyota Production System, alongside Just in Time (JIT).
While the term jidoka aims to impress people, the concepts that underpin it are far less common outside of Toyota. Perhaps this is because jidoka has so many distinct interpretations.
We’ll look at what jidoka is in this first installment.
What Is Jidoka?
Jidoka is a lean manufacturing technique in which machines automatically stop operating when they detect an abnormal situation.
Operators try to remedy the defect to avoid it from happening again. The term “autonomation” comes from the Japanese word “autonomy,” which combines the concepts of autonomy and automation.
Jidoka is a crucial pillar in the Toyota Production System (TPS), which eventually inspired the House of Lean.
Integrating intelligence into machinery allows a single operator to operate many machines with minimal effort. It makes businesses more valuable as efficiency increases.
The Principle of Jidoka Includes
To ensure that a company delivers defect-free products, Jidoka uses four simple principles:
- Find a flaw
- Put an end to the procedure.
- Fix the problem right off the bat.
- Find out what’s causing the problem and eradicate it.
These four processes can be used in various ways, depending on your industry. They can serve as a solid foundation for accomplishing continuous process improvement.
Anybody in your business can halt the process if they identify issues that jeopardize the quality of your product by using the Jidoka idea.
Jidoka is among the two pillars that have helped Toyota grow into today’s global powerhouse. Because it receives less attention than the JIT system, Jidoka is often the “forgotten pillar” of the Toyota manufacturing system.
Jidoka’s Origins
Jidoka was initially used in 1896 by Sakichi Toyoda, a Japanese innovator who eventually founded Toyota Motor Company.
It came in the form of a simple gadget that could stop an automatic loom’s shuttle if the thread snapped. The system was able to identify a broken line.
As a result, quickly shut down the machine and communicate a problem to avoid generating flaws. After that, the loom operator had to remedy the situation and resume the weaving operation.
What Are the Elements of Jidoka?
The Jidoka approach in lean manufacturing comprises four main elements: detection, stoppage, response, and prevention.
Having a solid grasp of these essential components can help you comprehend the theory and how you might implement it in modern manufacturing practices:
Detecting Errors:
Every piece of technology should have the ability to detect errors. Furthermore, you should implement an alert system. You do this to notify any abnormalities discovered, such as product faults, raw material mistakes, and machine breakdowns.
Production Cease:
Machines should be able to autonomously stop operating when an irregularity is detected to contain the problem. Operators should also be able to halt production if they see anything amiss manually.
Making Efforts:
Operators should examine the situation and seek support while using auto-stop methods that halt production. You should complete preventive steps within a specific deadline before deciding whether or not to continue production.
Keeping It From Happening Again:
When temporary remedies allow production to continue, managers should thoroughly investigate the issue to enact long-term solutions.
When the time limit expires, and the problem remains, a designated team should quickly investigate the root cause and resume production.
Jidoka In Lean Manufacturing
Jidoka necessitates a paradigm shift within the organization, from ignoring seemingly minor flaws in the name of achieving deadlines to accepting responsibility for assuring quality at the source.
Wherever the organization falls on that continuum, one thing is sure: the person is at the center of jidoka. People and machines functioning together are essential for successful deployment.
To begin jidoka’s performance in lean manufacturing, follow these three easy steps:
Establish Organizational Commitment:
Managers should treat Jidoka as seriously as Just-in-Time to set manufacturers up for success in implementing a lean manufacturing system (JIT). They frequently miss out on opportunities for expansion since they focus too much on maintaining a constant flow of labor and resources.
A comprehensive description should be developed and conveyed whenever management commits to implementing Jidoka. Because it is essentially a concept, everyone in the organization should be clear on it. The process begins at the top and works its way down.
Execute Readiness Evaluations:
Use a Jidoka checklist to assess particular implementation needs after receiving guidance from leadership to fundamentally change how the firm runs. Performing readiness assessments with appropriate stakeholders can help the organization better understand its current situation and prepare for modifications such as:
- Adjusting to a different revolutionary framework,
- Documenting specifications and requirements,
- Creating critical elements of the Jidoka performance
The goal here is to boost systems, such as evaluation, organizational learning, and innovation processes.
Implement Real-World Applications:
Plan and launch a specific Jidoka project with a cross-functional team after identifying and filling implementation gaps. Setting up machines or assembly lines with the ability to surface problems and stop output is one of the quickest methods to scale it.
Operators may quickly tell managers about difficulties using a visual management solution so that they can fix them right away. Earlier, when the machine stopped due to an error, the operator would restart it.
Staff members may now easily report safety or quality problems. Also, put strategies to avoid recurrence thanks to Jidoka’s practical implementation.
What Are the Benefits of Jidoka?
Jidoka offers numerous advantages because it is considered the most significant building element of lean manufacturing. They include the following:
- Jidoka lean manufacturing improves overall manufacturing process productivity by allowing for shorter and fewer production gaps.
- It significantly reduces the quantity of defective and damaged products to zero.
- It drastically lowers production costs, saves time and energy, and eliminates waste.
- Because it has a built-in quality control system, it improves product quality and, as a result, increases customer happiness.
- The issues are discovered early and handled immediately. It is to minimize further complications in the manufacturing process.
- It reduces the requirement for on-call inspectors because the technology can detect faults independently.
- Minor equipment malfunctions reduce the costs of equipment maintenance and servicing significantly. You can maximize your profits by using these savings in other aspects, such as enhancing process productivity.
- It lowers the need for additional staff because one person can effectively manage multiple machines simultaneously.
- Having the authority to stop production in a crisis boosts morale considerably.
- The prevention of problem recurrence adds to constant functioning and quality.
What Are Jidoka Examples?
It’s challenging to understand a topic without examples, and the Toyoda Model G automatic loom from 1925 is an excellent jidoka example.
Although this is common knowledge, we will demonstrate how it relates to jidoka. We will also show you a more recent jidoka example of a product you could already have.
Toyoda Automatic Loom Type G:
Sakichi Toyoda (1867–1930) created and patented the Toyoda Automatic Loom Type G in 1925. It is one of the many looms invented by the Emperor of Inventions, but it is the most well-known.
This loom may run nearly unattended. It is possible to perform routine operations like refilling yarns while the loom is in process and before it runs out. The loom may also detect and shut down faults. A worker with no experience may readily handle thirty to fifty looms.
This loom was most likely the most innovative loom available. The model was so popular that Toyoda licensed it to other manufacturers. Now we will explain the loom’s tricks.
These are excellent examples of jidoka’s outcome: halt the activity immediately and correct the problem whenever a problem arises.
Warp Brake Auto Stop:
Warp Brake Auto Stop was a unique function. A warp is a collection of parallel strings through which a weft gets weaved. It is imperative to repair the warp promptly if it breaks. The inferior the cloth made, the longer an automatic loom generates with a damaged string.
In the past, a worker – typically a youngster with lower wages than an adult – was required to oversee machinery constantly. The intention was to rapidly re-tie the warp if it broke. It is not a good mix for children to operate moving machinery with little regard for their safety.
There was a unique feature on the Toyoda Automatic Loom Model G. Every warp has a sheet metal piece dangling from it. The warp tension held up the sheet metal, and if the warp snapped, the sheet metal would drop a few centimeters.
A bar beneath the sheet metal was connected to the shuttle action and moved back and forth in a rhythmic pattern. There was adequate room for this bar to travel as long as the warps remained intact.
However, when a warp broke and fell, it stopped the bar from moving. The loom was promptly stopped and prevented from creating substandard cloth due to the blocking of the movement.
The gleaming metal rods allowed the sheet metal to fall a certain distance. While also holding it in place when the moving bar tried to shove it out of the way.
Jidoka gets exemplified in this situation. If an error occurs, the machine will instantly stop. In addition, if the weft breaks, Model G contains a stopper.
Jidoka and Its Importance
Jidoka is a crucial component of the Toyota Production System and Lean. Toyota can only accomplish its current level of success by integrating Jidoka, respect for people, and Just in Time (JIT) principles.
Many western organizations are attempting to apply Lean fail to give their personnel and machines the power to stop the entire production line if a problem arises. Hence, do not create the sense of urgency and discipline required to address the core causes of our many issues.
A JIT system necessitates the reliability of all process components and the production of defect-free products when needed. Enable people to fix issues whenever. Jidoka devices emphasize them because any failure will lead the system to break down.
By incorporating Jidoka into your Lean system, you may start eliminating problems from your processes and achieving considerably higher quality. Jidoka will usually generate better results than the frequently mentioned Six Sigma quality levels.
What Makes Jidoka So Tricky?
Identifying a problem or even halting a machine is not the actual issue for jidoka, and it’s all about what happens afterward. A well-designed machine stops whenever a problem occurs, but the operator clears the issue and restarts the unit.
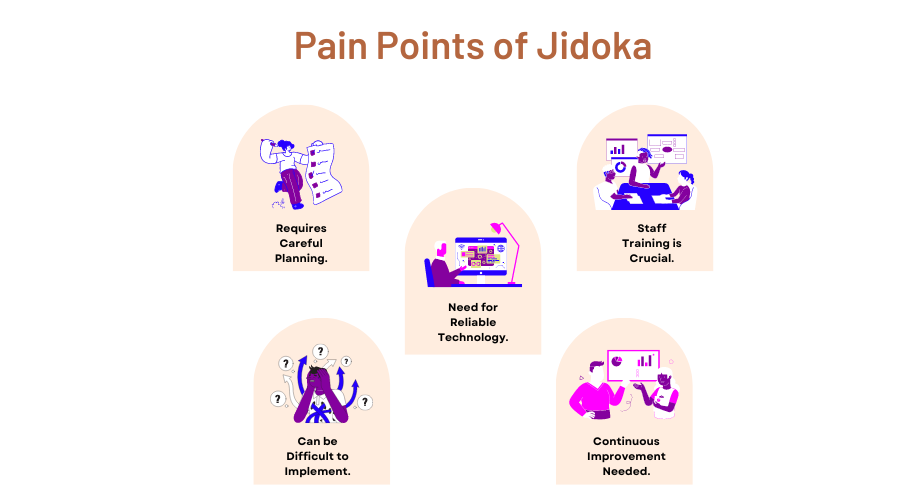
The following is the key to continual improvement success:
Resolve the issues you notice as soon as possible.
Since so many minor issues need fixation, executives generally focus on the significant wins. Additionally, commit their continuous improvement efforts to substantial initiatives.
In most cases, there are two steps to this procedure.
The first is a temporary solution. You must quickly deploy an inspection phase or a test station to prevent problems from escaping. You won’t just be able to fix the problem right away, but you can get the line back in operation once you do.
The second step involves a more refined approach to issue solving. It requires a fundamental cause analysis to pinpoint the specific source of the problem and a long-term solution to prevent relapse.
Conclusion
Jidoka has various definitions in the lean manufacturing world. In general, it refers to a machine or equipment that stops itself when there is an abnormality. It also refers to detecting or checking errors by the operator and preventing production when anomalies are detected.
Jidoka is the foundation for Toyota’s and Lean manufacturing’s Error-Proofing process.
The concept plays a vital role in reducing defects at the root cause (i.e., preventing defects from ever occurring). It reduces work, expedites problem resolution, halts processes in a controlled manner, and helps troubleshoot effectively to achieve quality.
At the same time, jidoka can seem like a difficult concept to embrace, especially at first glance. Because it appears counterproductive to lean manufacturing practices.
With a bit of exercise of the imagination, we can see its benefits in many situations. Jidoka is indeed an interesting concept. Hope this article has guided you to gain a deeper understanding of one of the pillars of lean manufacturing.