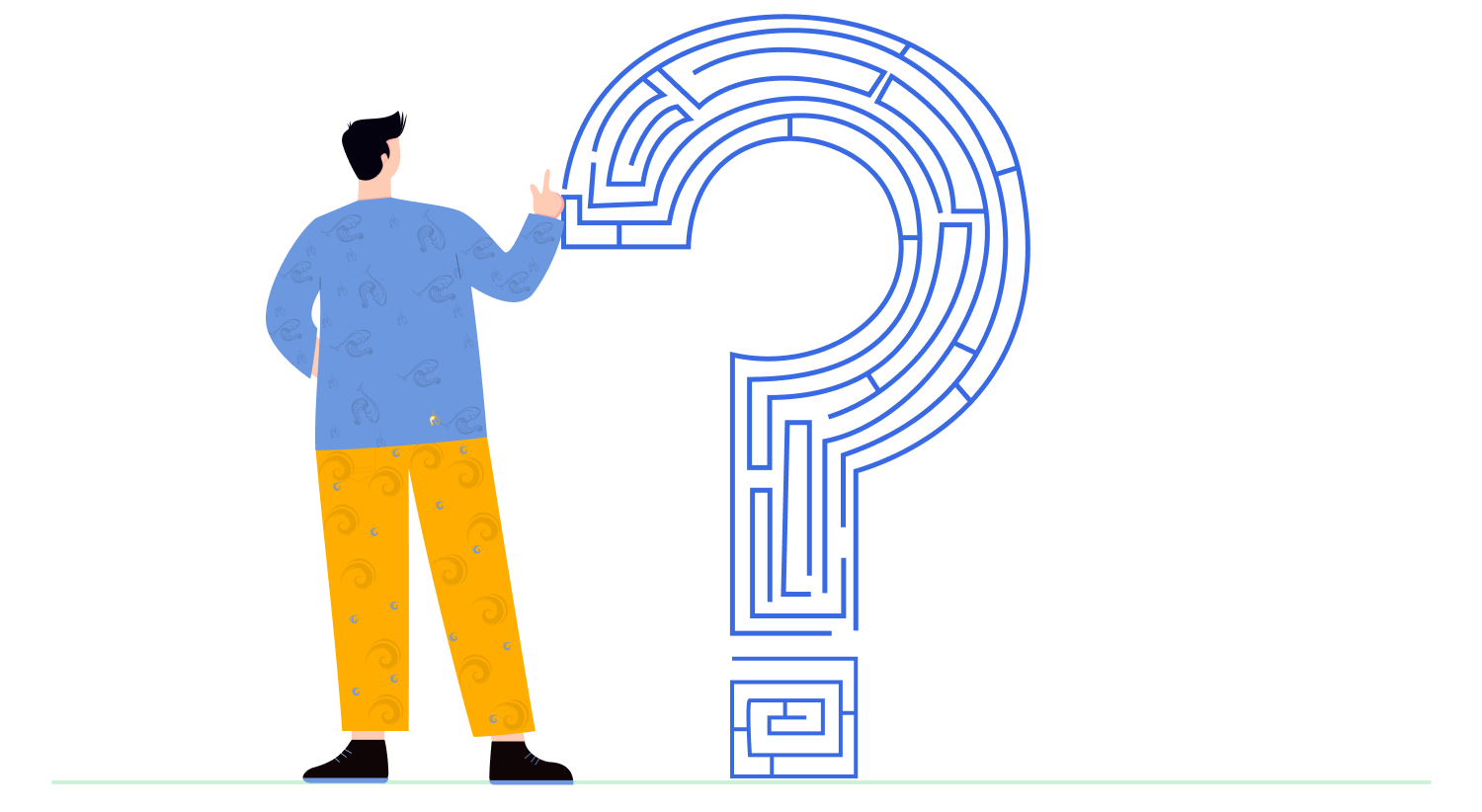
What are 5 Whys?
Definition of 5 Whys
One of the most powerful root cause analysis tools in the Lean management armory is the 5 Whys technique. In their everyday job, every team encounters hurdles. Using the 5 Whys, on the other hand, will assist you in identifying the core cause of any issue and safeguarding the process from repeat errors and failures.
Five whys (5 whys) is an interrogation technique used to identify the root cause of any problem. As the name suggests, it investigates the cause and effect relationship underlying any given situation. It consists of 5 why-questions to find a solution and resolve the issue.
This interrogative technique was invented in Japan in the 1930s by Sakichi Toyoda, who used it within the Toyota Motor Corporation.
It is an essential component of problem-solving training. The Toyota company still uses this technique for problem-solving, as do many other companies.
Purpose of Five Whys Method
The five reasons technique is a problem-solving tactic used to improve the product’s quality and solve issues that don’t have an immediate or apparent cause. This technique performs efficiently with problems that have moderate or straightforward difficulty. For example, our landing page CTA isn’t converting. Why?
However, you cannot use them for complicated problems. That’s because many different parts need to get assessed for complex issues.
Moreover, there might be more than one cause for the surface issue, and have a lot of branches to be explored. Thus, it can cause a lot of inconvenience with complex problems.
You can use alternative techniques like cause and effect analysis instead to solve such problems.
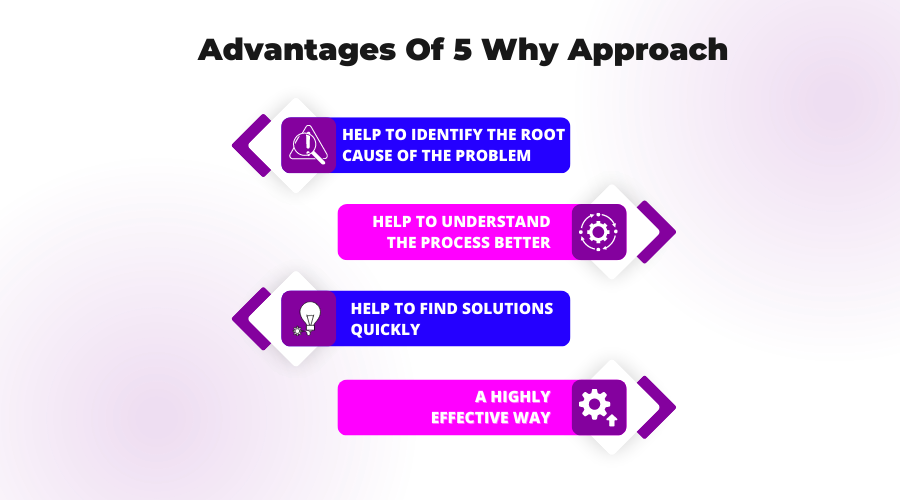
How to Conduct 5 Whys Analysis?
Some of the steps to exercise the 5 whys are as follows:
First step
The problem-solving process starts with establishing rapport with the problem and familiarizing oneself with the product and the affected parts.
One of the team members acts as a facilitator. That is to ensure that the group is focused on the problem and works to find the solution.
You must write a problem statement to understand the problem and define the issue so that everyone agrees.
Second step
The second step starts with asking the first-why question – ‘Why has the problem occurred?’ For instance, “Why don’t we make sales?”
The objective of this question is to find a precise answer about the occurrence based on observation and insights.
There is no way to estimate it, and instead, you ought to identify one apparent cause. It’s best to go on to the following stage if you’ve found two or more answers to this question.
Third step
This step requires asking the other four whys and finding their answers. Considering the same example of the first-why, here is how the other four why’s can form.
First why?: We don’t make sales.
Second why?: We have less advertisement
Third why?: We have poor quality graphics
Fourth why?: The team is not well-trained
Fifth why?: We have low budget
And voila! You have your root cause traced to the lower budget and the need for increased funding. This way, you can ask the 5 whys to find the root cause of the problem and, ultimately, a solution to the root cause.
Best Example of 5 Whys
Let us look at a 5 whys example to gain a better understanding.
Problem statement: The client notices an issue during User Acceptance Testing (UAT).
1. What has caused the client’s problem?
As per the technical lead, the testing team has not raised any issues with the development team.
2. Why was the issue not caught by the testing team?
Only sanity testing gets done, not complete regression testing.
3. Why do only sanity tests by the testing team?
They didn’t have enough time to test the entire program thoroughly because they didn’t have enough time.
4. Why wasn’t there enough time to conduct comprehensive functional testing?
Because the build arrived one day before UAT, complete functional testing takes at least three days.
5. Why was the build only made available one day before the UAT?
As we saw, the development team took longer than expected to fix a few flaws.
We can observe that there are two root causes in this case rather than one:
The first root cause is that team members could not provide accurate estimates for their functionalities, necessitating training in estimation approaches and their application.
The second root cause is a problem with project management because, in theory, a code freeze should occur at least four days before the UAT. Yet, the team worked on bug fixes until the last day.
What Is the 5 Whys Method Template?
A 5 Whys template is a structured format that guides individuals or teams through identifying the root cause of a problem. Here’s how you can use it for effective problem-solving:
Step 1: Gather the Right Stakeholders
It’s essential to have the right stakeholders involved in the brainstorming process. Key decision-makers should be present to ensure the discussion is productive and effective.
Step 2: Choose a Moderator
Assign a moderator to ensure that the conversation stays on track and assumptions are avoided. The moderator should drive the conversation and follow all the process steps. It’s best to select someone with experience with the technique or who is naturally curious.
Step 3: Establish a Problem Statement
Start by creating a clear problem statement that explains the issue your team needs to address in 1-2 sentences. You need to add this statement to the 5 Whys template.
Step 4: Initiate With an Inclusive and Open-Ended Question
Using the template to structure your brainstorming discussions, start with the broadest possible question. In this step, ask the group to think about the problem statement and what contributed to it.
Step 5: Refine the Question and Pose It Again
Narrow down the question from Step 4 and ask again to see where it leads. Follow the 5 Whys template and ask why up to three more times. Each answer will narrow down the potential root cause of the problem.
Step 6: Discussion of the Root Causes
Once you’ve asked why up to five times, you may find that you have uncovered the potential causes of the problem. The discussion should focus on these causes and how they contribute to the problem.
Step 7: Suggest Solutions
As you uncover the causes of the problem, you will also come up with potential solutions. Your team will likely devise more solutions as the questions become more specific. Record these solutions on a whiteboard or a kanban board and assign owners and the next steps to follow up.
Practical Example
Let us use the above 5 why template guide and understand it with a 5 whys example.
Problem: You have a headache.
- Why (do you have a headache)? – Because you didn’t get enough sleep last night.
- Why (didn’t you get enough sleep)? – Because you were working late on a project.
- Why (were you working late on a project)? – Because you underestimated the time required to complete it.
- Why (did you underestimate the time required)? – Because you didn’t break the project down into smaller tasks.
- Why (didn’t you break the project down into smaller tasks)? – Because you didn’t have a clear plan or strategy for managing your workload.
In this example, the root cause is that the person needed a clear plan or strategy for managing their workload, which led to working late, not getting enough sleep, and ultimately, a headache. Once this root cause gets identified, potential solutions can be discussed, such as creating a more structured plan for managing tasks and projects or seeking help from a colleague or manager.
5 Whys Root Cause Analysis Disadvantages
One of the main disadvantages of using the 5 Whys root cause analysis (RCA) approach is that it assumes only one root cause of a defect. The situation may be much more complex, with multiple root causes to consider.
Therefore, it is essential to examine all aspects related to the defect and consider all potential root causes.
Another limitation of 5 Whys root cause analysis is that organizations often only use it to identify negative issues within their operations.
However, 5 Whys root cause analysis can also identify positive aspects and why specific processes perform exceptionally well. By identifying positive points, organizations can find more opportunities for continuous improvement and enhance their overall performance.
What Are the Challenges Faced While Performing the Five Whys?
Often, the number of questions asked to get to the real problem is not just five, and it requires other perspectives to understand the cause of the problem.
In such a case, there may be the need to ask “what,” “how,” and “where” for the best solution.
Another challenge in 5 whys is that teams don’t know the boundary of when to stop asking questions. They may keep going on and on in a vicious circle without finding a valuable response for the solution.
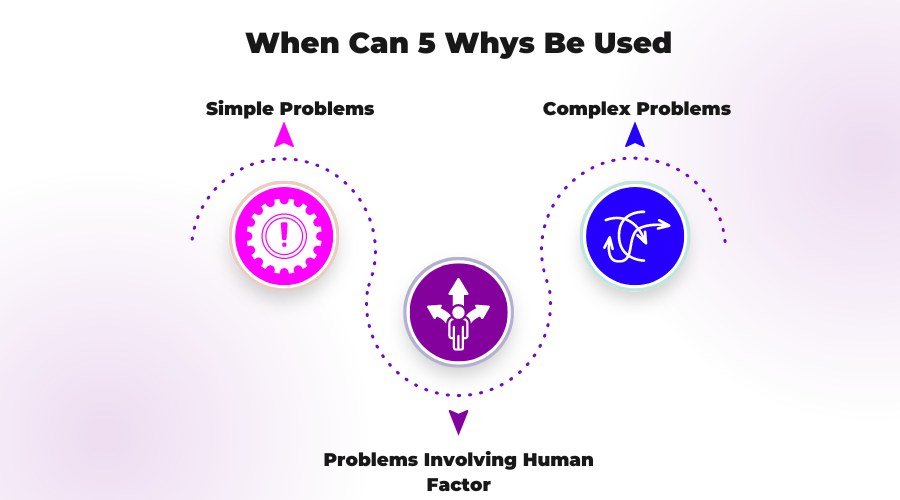
You may also be interested in:
FAQs
The five whys is an interrogative technique invented by Sakichi Toyoda, who used it in Japan in the 1930s. The Toyota Motor Corporation employed it.
Five whys crucial to improve the product’s quality and solve issues that don’t have an immediate or an apparent cause. This approach is important for implementing product management tools for product managers. This technique performs well with problems that have moderate or straightforward difficulty.
Asking “Why?” five times is part of the “5 Whys” problem-solving technique, which helps you find the source of an issue. You can create and implement a countermeasure to stop the issue from reoccurring once you’ve determined the underlying cause. By systematically identifying and addressing the underlying causes of a problem, the 5 Whys technique helps to improve processes and increase efficiency