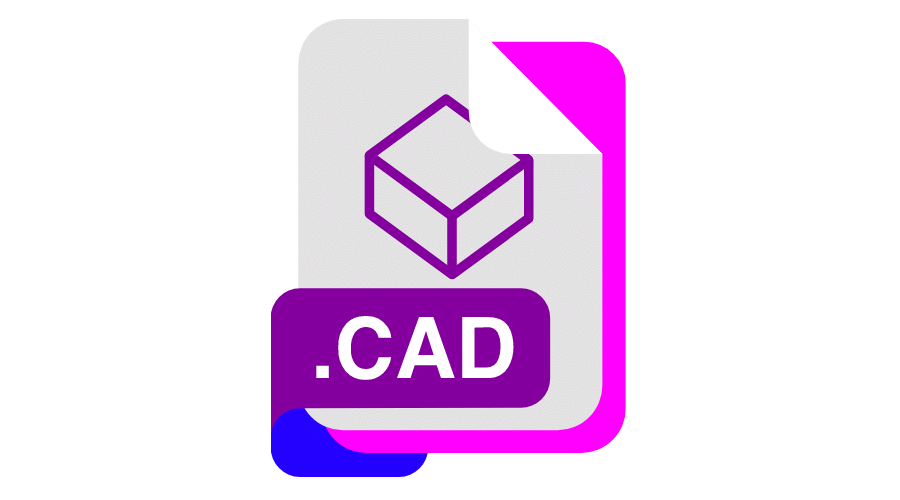
What Is CAD and CAE?
Ever wondered how engineers design incredibly complex products like airplanes, cars and prosthetic limbs? They rely on some handy software tools called CAD and CAE.
CAD/CAE are software used in product design modeling. CAD is Computer Aided Design. It is used to make 2-D or 3-D designs of products through computers. CAD is widely used in animation, architectural designs, mechanical designs, etc., to create and modify 2-D or 3-D design models.
CAD refers to programs that allow users to create 3D digital models and 2D technical drawings of components. Sketching by hand is a thing of the past – instead, engineers design precisely to scale using CAD. Popular options include AutoCAD, SolidWorks and Inventor.
CAE is computer-aided engineering. This involves using software apps for engineering analysis and testing of the design or product. CAE helps the designer in product testing by providing virtual simulations for field experiences.
CAE programs take CAD models and enable engineers to simulate and analyze how their virtual designs will perform in real life. CAE software helps detect and prevent issues early on. For example, is the part strong enough? How will airflow affect performance? Will it endure high stresses?
Together, CAD and CAE empower engineering teams to repeatedly refine designs until they’re optimized. Complex workflows become easier to manage too since the digital models integrate various physics analyses. The end result? Better, safer, more efficient products that make it from conception to mass production on time and on budget.
So in summary, while CAD focuses on digitally drawing up designs, CAE uses those same virtual models to rigorously test simulated performance – drastically improving methods compared to the old-school paper drafting table!
The Differences Between CAD and CAE
The Differences Between CAD and CAE are as follows
- Design vs Simulation – CAD is for designing and drawing up 3D models, while CAE takes those designs and simulates their performance.
- Focus – CAD focuses on digital design and drawings. CAE analyses how the design will behave in real world conditions.
- Input – CAD requires engineering sketches and specifications as input. CAE uses the CAD model and additional simulation parameters.
- Output – CAD outputs 3D models and technical drawings. CAE produces simulation results that reveal things like stresses, deflections, thermal effects etc.
- Complexity – CAD can handle simpler models, while CAE deals with complex simulations of multiple real-world factors like aerodynamics.
- Validation – CAD validates proper geometry and specifications. CAE validates if the design will operate as intended before physical testing.
- Teams – CAD users are mainly designers. CAE users include engineers running simulations to optimize performance.
- Timing – CAD is used earlier in development. CAE comes later to validate designs before prototyping.
In summary, while closely integrated, CAD focuses on design creation and CAE on validating designs through sophisticated simulation analysis before manufacturing. Used together, they speed product development cycles.
Importance of CAD and CAE in Modern Product Development
CAD and CAE Are Essential Tools for Product Developers Today. Engineering teams rely heavily on CAD and CAE software to help deliver high-quality, innovative products faster than ever before.
Here are some key ways these digital design and simulation tools make such a big impact:
- Faster iterations – Being able to design, test, and refine concepts virtually eliminates the delays of physical prototyping. This drastically speeds up getting ideas out the door.
- Real savings – Fewer physical builds means huge savings on manufacturing costs. Early CAE analyses also prevent costly reworks mid-production.
- Better collaboration – Distributed team members seamlessly collaborate through shared access to models anytime, anywhere via the cloud.
- More responsive to change – Late modifications don’t spell disaster now. Digital changes are simple, giving products room to evolve up until production.
- Catching issues early – Thorough CAE testing catches structural, fluid, and other problems at the design stage before building bad prototypes or worse, faulty end products.
- Facilitating innovation – Engineers can experiment freely with more ambitious designs that may have previously been impractical through prototyping alone.
- Meeting regulations – Quantitative CAE data satisfies the rigorous documentation needs of industries like aerospace, medical, and automotive to speed safety approvals.
- Training the next generation – Young engineers entering the workforce already have hands-on experience with our digital design future through using industry-leading CAD and CAE packages in school.
Overall, effectively utilizing these advanced tools is now imperative for optimizing modern product development processes and delivering with excellence to customers who expect world-class solutions.
Benefits of Using CAD and CAE
The Awesome Perks of Using CAD and CAE
- Faster designing is so clutch – With CAD, you can whip up way more iterations in no time without waiting for slow prototypes.
- Save big bucks – Using CAD and CAE means way fewer physical builds, saving thousands in manufacturing costs. Bonus – virtual testing prevents reworks too.
- Catch issues up front – CAE simulations find structural flaws and other problems at the design stage before wasting time and cash on broken prototypes.
- Protect customers – Thorough virtual testing helps ensure products won’t fail out in the real world, keeping customers safe and happy.
- Cloud collaboration FTW – Teams worldwide sync up via the cloud on projects together seamlessly from anywhere 24/7.
- No sweat changes – Updates are easy-peasy digitally versus expensive physical remakes if tweaks are needed later on.
- Meet regulations seamlessly – CAE data proves to regulators that high-risk designs like aircraft and medical devices perform as planned.
- Lifted innovation – Engineers now experiment freely with even crazier ideas that would’ve been too difficult to prototype originally.
- Students stay ahead – Our future design stars get real-world practice with the pro tools they’ll use on the job like SolidWorks and ANSYS.
- Global teams rock – International partnerships flow smoothly when everyone works on the same digital models remotely.
In short, CAD and CAE empower engineering teams to reduce risks, optimize solutions for performance and value, and rapidly get high-quality products to eager customers through more streamlined development cycles.
For Designers and Engineers:
- Faster Designs – Digital tools mean creators can whip up iterations in no time instead of waiting for physical models.
- Early Testing – Engineers catch flaws virtually before building prototypes so changes are cheaper.
- Enhanced Collaboration – Teams globally work together seamlessly from anywhere via the cloud on one digital master file.
- Simpler Changes – Late tweaks aren’t so costly or disruptive when done in CAD vs. on physical parts already made.
- Safer Products – Thorough CAE analysis helps ensure designs won’t fail when manufactured or in customers’ hands.
- Regulatory Compliance – Quantitative performance data eases approvals for things like medical devices and aircraft.
- Sped Innovation – Creators can experiment freely with ambitious concepts that may have been too complex without CAE virtual testing.
- Career Development – Designers learn essential industry-standard skills on CAD/CAE platforms they’ll use for decades.
- Project Optimization – Virtual prototyping facilitates multiple design iterations for ideal solutions.
- Client Delight – Faster deliverables and performance-tested products reliably impress even the toughest customers!
By leveraging digital design and simulation tools, product dev teams create optimal solutions customers adore.
For Businesses:
When it comes to product development, using computer-aided design (CAD) and computer-aided engineering (CAE) software can provide huge advantages over old-school manual design methods. Here are the top 10 ways CAD and CAE can benefit your business:
- Speed up design cycles. With CAD, you can rapidly test different design concepts virtually before building expensive physical prototypes. This allows you to iterate more efficiently.
- Reduce costs. CAD/CAE means less wasted spend on making faulty prototypes. You can catch design flaws earlier using virtual simulations, saving money versus fixing real-world issues late in development.
- Improve quality. Integrated CAD and CAE enables more thorough testing of products virtually. This leads to fewer defects sneaking through to manufacturing as more scenarios can be modeled on screen.
- Foster collaboration. Cloud-based CAD software makes it easy for geographically dispersed design teams to work simultaneously on projects from anywhere. Real-time feedback is also possible.
- Ensure regulatory compliance. CAE simulations allow you to prove a design meets standards for factors like structural integrity, durability, emissions, and safety before building physical prototypes – saving rework.
- Analyze alternatives rapidly. “What if” scenarios can be evaluated easily using parametric CAD models. Quickly assess multiple design or materials options without rebuilding each time.
- Archive design history. CAD files and CAE analyses are digitally stored, providing clear documentation of a product’s evolution for future reference, repairs, or regulatory inquiries.
- Appeal to tech-savvy customers. Sophisticated CAD renders and animations used in marketing give products a high-tech image that resonates with many buyers today.
- Train less experienced users. Through easy to learn tutorials, CAD software empowers novices to rapidly acquire skills otherwise needing apprenticeships or coursework.
- Gain a competitive edge. Adopting cutting-edge CAD/CAE positions businesses as innovative leaders, attractive to talent, customers and strategic partners alike. Stay ahead of industry trends.
In summary, using computer-based design and testing tools delivers immense value that traditional methods alone cannot match for product development in today’s marketplace.
Popular CAD and CAE Software
Whether you’re designing a new product or analyzing an existing one, CAD and CAE software plays a key role. But with so many options out there, which programs should be at the top of your list? Here are the most commonly used based on our experience:
- AutoCAD – The granddaddy of them all, AutoCAD has been a workhorse in engineering offices for decades. While its interface may seem dated compared to competitors, its 2D drawing tools are second to none. Great for basic drafting tasks.
- SolidWorks – For solid modeling and 3D design, SolidWorks is the gold standard. It’s easy to learn yet powerful, supporting everything from concept sketching to detailed assembly modeling. The CAMWorks add-on also enables CNC programming right from the model.
- ANSYS – When it comes to complex finite element analysis, ANSYS is king. Its suite of simulation tools can model nearly any engineering problem you throw at it, from basic statics/dynamics to CFD, electromagnetics, explicit dynamics and more. Completely customizable workflows.
- Altair HyperWorks – A good intermediate option between ANSYS and smaller FEA programs, HyperWorks offers best-in-class solutions for vibration/acoustics, durability and topology optimization. The preprocessing interface beats competitors hands down in our view.
- PTC Creo – As both a CAD and PLM powerhouse, Creo seeks to be an all-in-one solution. While its diverse capabilities are compelling, some complain the interface feels convoluted compared to SolidWorks. Steep learning curve.
- Siemens NX – Like Creo, NX straddles both CAD and PLM. It really shines for complex surface and direct modeling workflows. Steep cost of entry limits its popularity relative to SolidWorks in many smaller firms.
We hope this gives you a sense of the core programs used across engineering today. As always, it’s best to test drive the trial versions to see what interface and tools suit your needs best.
FAQs
In CAE simulation, CAE software tests the product by providing virtual situations of the field conditions and environment that the product will have to endure.
Some examples of CAD and CAE software are CAD- AutoCAD, TinkerCAD, Solidworks, etc.
For CAE- MATLAB, Simulink, Fusion360, etc.
The significant difference between computer-aided design and computer-aided engineering is that CAD is software used to build a product design, and CAE software is used to test and analyze the product through simulation.