What Is a Kanban Card & How Does It Control Inventory?
June 7, 2022 Max 7min read
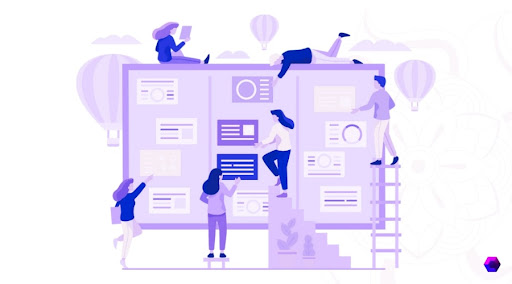
What Is a Kanban Card?
Kanban card definition:
A Kanban card depicts a work item in visual form. It translates to “visual (kan) card (ban) in Japanese. It’s an essential part of the Kanban system because it indicates work that’s been requested or is already underway. A kanban card is a little card that contains information about a specific part used in production. It’s a signal from upstream advising someone to move, buy, or produce more of a component for manufacturing.
All of this began in the early 1940s. Taiichi Ohno (Industrial Engineer and Businessman) created the first Kanban system for Toyota Automotive in Japan. It started as a simple planning system to optimally control and manage work and inventory at every production stage.
As the technology industry grew in the 1990s, management consultant David J. Anderson developed the Kanban Method, which applied lean principles to more intangible knowledge work such as information technology and software development.
You may utilize your device screen to visualize, manage, and collaborate in real-time with your team using an online Kanban board. Online Kanban boards mimic the whiteboard or bulletin board format by using apps, but they offer a lot more: flexibility, faster productivity, clarity, and transparency.
The low productivity and efficiency of Toyota in comparison to its American automotive rivals was a driving force behind the origin of Kanban.
Toyota used Kanban to make up a flexible and efficient just-in-time production control system that enhanced productivity while eliminating costly raw material, semi-finished material, and completed product inventory.
The kanban card and the kanban board, at its foundation, promote teamwork by allowing team members to interact and share information visually.
“The two pillars of the Toyota manufacturing system are just-in-time and automation with a human touch, or autonomy,” Anderson once stated.
Continue reading to grasp more about setting up and running a Kanban inventory management system to enhance your productivity, output, and product quality.
What Are the Types of Kanban Cards?
The cards serve as a signaling mechanism, moving back and forth between the various stages of the manufacturing process. In most kanban systems, several distinct types of cards are present.
Conveyance or Withdrawal Kanban Cards
These are a type of management system. They notify individuals when a portion in one area completes. Many production lines require items to be worked on in one place for some time before being moved to the next. This card indicates that parts are ready to be transferred.
Teams use withdrawal cards or movement cards to notify people when an item is ready to be moved from one part to another. When the unit sets for new work, they send the withdrawal card to the preceding division. In addition, the card often indicates the number of things that you must transport to the location where they are required.
Kanban System for Suppliers
A supplier kanban goes directly to a supplier — a company that supplies goods to the manufacturer — and registers as a manufacturer representative in the supplier’s kanban system.
The supplier cards speed up the procedure by eliminating the considerable wait times associated with submitting a supply request. Instead of sending a request to procurement and waiting for it to pass, teams can engage directly with suppliers and obtain the things and resources they require without further delay.
Kanban Cards for Emergencies
When anything is broken or has a problem, these cards are used. When a problem with a single item or a series of parts is in light, the emergency Kanban card is delivered to the prior station so that they are aware of the issue.
If the problem is severe, the emergency card can even instruct the entire team to halt working so that there is no backup while the section dealing with the problematic items deals with the problem. As a result, teams will produce less waste, and the production will continue to function smoothly.
Express Kanbans
When unanticipated shortages of parts develop, express kanbans notify the need for more of a specific position so that the manufacturing process does not slow down.
As we know from above, teams can send out emergency cards if their supplies run out (very quickly) or if production needs to slow. In extreme instances, emergency cards may call for a complete shutdown of production until specified items or parts supply.
Express cards, like emergency cards, are essential for maintaining a continual process flow and guaranteeing that the process does not slow down or stop.
Production Kanban Cards
This type of Kanban card usually contains a list of all the essential parts at any particular time. The workstation sends a production card to a facility area, seeking the required resources (or tasks).
The production Kanban card activates the production system, indicating the quality and quantity of the items to be produced. In addition, the manufacturing cards carry information from the Kanban card pullout.
Through Kanbans
These are a hybrid of withdrawal and production kanbans used to speed up production when the two work centers for these kanbans are next to each other.
The teams would utilize a single card to indicate both of their actions, which saves time and improves productivity.
How Do Kanban Cards Work?
In product management, each kanban card symbolizes a single work item as it progresses through several stages of completion on a real or virtual kanban board.
Imagine a software development team utilizing sticky notes on a whiteboard to indicate their job items to understand what kanban cards are. The group pushes the sticky notes through the columns labeled Prioritized, Design, Development, Testing, Blocked, and Done as they work on issues and features.
How To Use Kanban Cards for Inventory Control?
Kanban inventory management is essentially a method of keeping only the bare minimum of stock on hand at any given time. This prevents buying more than you need and finding a place to store the excess inventory. Kanban is also a method of avoiding bottlenecks in your workflow.
A corporation can use Kanban cards or bins to communicate when stock needs a refill in a Kanban inventory system. Companies use visual cues to initiate the restocking process in the Kanban bin system. Workers are given two inventory containers and must go through the supplies in one before moving on to the other.
How Many Kanban Cards Are Needed?
Choosing how many cards to utilize is one of the most fundamental questions in Kanban system design.
Unlike typical “push” systems, which transport stuff downstream on a schedule or “shove” things downstream even if the downstream partner isn’t ready, a “pull” system fosters and nearly requires cooperation from a systems perspective.
Congestion is also caused by “pushing,” which develops exponentially as more items add to the queue. A “pull” system removes overproduction, underproduction, work-in-process, inventory, and cooperation and coordination. The Kanban is a critical component that supports “pull” in a system.
You’ll need to do simple math to figure out how many cards and how often Kanban withdrawals happen. The general guideline is as follows:
How To Calculate Kanban Cards?
You’ll need to do simple math to figure out how many cards and how often Kanban withdrawals happen. When considering the amount of Kanbans, remember the following general rule:
N = DT(1+X)/C
Where,
N stands for the number of cards.
D stands for demand per unit of time.
T stands for lead time, C for container capacity, and X stands for a buffer or safety factor.
Workgroups must establish how many Kanban cards are required to correctly manage a process, which might vary contingent on the type of project, the complexity, and the number of team members.
Because Kanban is all about figuring out what works best, deciding how many cards to use is an iterative process. The three-step procedure described earlier is an intelligent way to figure out how many Kanban cards you’ll need.
Wanna Know the Best Kanban Tool?
A good Kanban board tool can make a big difference in your team’s performance and progress. A Kanban application allows teams to see where they spend their time and provides analysis to identify and fix concerns quickly.
Here’s a rundown of the finest Kanban board software:
Chisel’s goal is to assist you in creating excellent products. We think that there are three critical elements to creating outstanding products: producing the right product at the right time, aligning the team, and establishing a deep, direct customer relationship.
Chisel meets all these elements. The tool’s Kanban capability is critical, and it’s simple to build up products to manage tasks.
Many people choose Chisel as their tool of choice.
Check out our website and try Chisel today.
FAQs
A Kanban card contains important information about the work and its progress, such as a summary of the assignment, the person responsible for it, the deadline, and so on.
A kanban card is a little card that contains information on a particular production element. It’s a signal from upstream that advises someone to move, buy, or produce more of a component for manufacturing. The number of units (things, pounds, kits, etc.) that require action must be on these cards.